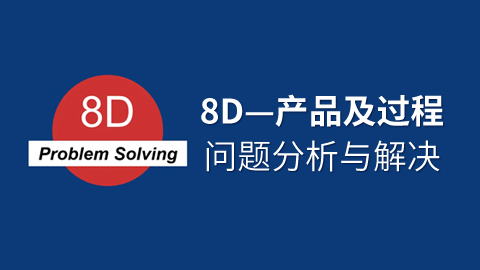
宣讲主题
其他
宣讲形式
其他
课程简介
8D—产品及过程问题分析与解决
【课程背景】
产品品质是决定市场及品牌的根本保证,在现今竞争激烈和成本不断提升的市场环境下,企业能够有效处理品质问题并避免再次发生,以不断提升顾客满意度,是赢得市场、降低成本的实效方法。
8D是最早在福特公司实行的品质管制及改善的特殊必备方法,之后已成为QS9000/ ISO TS16949、福特公司的特殊要求,并逐渐发展成为一个固定而有共识的标准化问题解决步骤。
8D是有效解决问题的的管理工具,能系统、逻辑的分析和解决生产现场中的质量问题,是在汽车产业、组装及其他产业中,利用团队方式结构性彻底解决问题时的标准作法,通过对工具方法的应用达成提升质量的目标。
【课程目标】
1.掌握8D分解和解决问题的工具、步骤与流程;
2.全面提升企业生产、质量、设备管理的水平。
【课程对象】
生产企业质量、生产及相关岗位的管理者。
【培训时间】
1天(6小时/天)
【培训方式】
案例分析+实践演练+提问互动+分组讨论+咨询指导,教练技术贯穿课程始终
【培训效果落地输出】
1.培训现场输出
1)课堂上学员小组演练,汇集集体智慧的教学问题解决方案;
2)系统、结构化的认知思维输出;
3)企业个性要求融入课程,提升认知或解决方案的输出。
2.课后落地
1)针对培训主题并结合岗位工作的反思与总结;
2)课程应用计划任务布置。
【课程大纲】
启发开篇:
1.不同部门的质量责任
2.纠正、纠正措施、预防措施
第一单元 8D基础认知
一、8D的本质
1.重要术语
2.8D起源与适用范围
3.8D的目标与作用
1)为什么要推行8D
2)启动的时机与步骤
二、8D工作方法与流程
第二单元 征兆/紧急反应措施(ERA)——DO
一、应急反应措施三原则
1.确定是否需要反应行动
2.验证、执行紧急反应行动
3.确定是否需要8D
二、D0阶段的常见问题
小组练习:交付产品与顾客提供样件不一致顾客拒收
第三单元 成立小组——D1
一、成立小组的目标
1.小组成员选择
2.小组成员的职责
3.小组操作程序和协作
4.小组成员的知识
小组活动:组织与计划
二、小组成功的关键要点
互动讨论:小组履行职责的障碍与关键
第四单元 描述问题——D2
一、描述问题的目的
1.掌握信息
2.共同的管理语言
3.拟定清晰目标
二、 问题描述关键要点
1.数据
2.问题拆解与细分
3.聚焦现状,确定范围
三、问题描述的原则与方法
1.对象明确
2.可观察,可测量
3.简洁
小组活动:描述问题
第五单元 实施并验证临时性措施(ICA)——D3
一、与D0的差异
1.维护系统正常运行
2.争取时间
3.保护客户权益
4.减少不良品发生
二、临时解决方案的四个步骤
1.选择ICA
2.验证ICA(措施)
3.执行ICA
4.验证ICA(效果)
小组活动:ICA制定
第六单元 确定和验证问题的根本原因——D4
案例:更换零部件真的解决问题了吗?
一、为什么要验证根本原因
1.防止反复故障出现
2.不必要浪费时间在失效控制上
3.确保顾客满意度
4.一劳永逸
二、确定根本原因
1.鱼骨图法
2.5Why法
3.关联图法
小组练习:寻找根本原因
三、验证根本原因
1.末端验证
2.测试、实验取得数据
第七单元 选择/验证长期纠正措施(PCA)——D5
一、为什么要选择/验证长期纠正措施
二、选择长期纠正措施
1.列出决策标准
2.确定满足标准的相对重要性
3.选择和决策标准
4.分析风险
5.最佳选择
三、验证长期措施
1.验证的方式
2.验证风险分析
小组活动:建立纠正措施计划
第八单元 执行和证实PCA——D6
一、执行和证实PCA目的
1.消除故障的根本原因
2.确保PCA执行有效
二、执行PCA
三、验证PCA
1.问题是否被彻底解决
2.客户跟踪
小组活动:验证纠正措施
第九单元 防止问题再次发生——D7
一、针对长期纠正措施验证的结果
1.固化长期措施为标准
2.橫展类似产品/工艺
二、关键事项
1.现场确认
2.效果是否维持在良好水平
小组活动:预防再发生的有效措施
第十单元 表彰小组和个人的贡献——D8
一、表彰的价值
1.过程结束
2.建立团队自信
3.鼓励参与
二、表彰的特点及方式
三、8D报告
1.编写要求
2.报告格式
3.内容组织
第十一单元 8D工具使用常见的问题与对策
一、解决问题的思维误区
二、常见问题与对策
1.领导不重视
2.标准化基础差
3.无有效激励机制
4.工具工艺知识欠缺
5.企业内部协同能力不足
授课时间
不限
现场所需设备
投影(LED)/电脑/
交通
需要接送
发表评论 取消回复